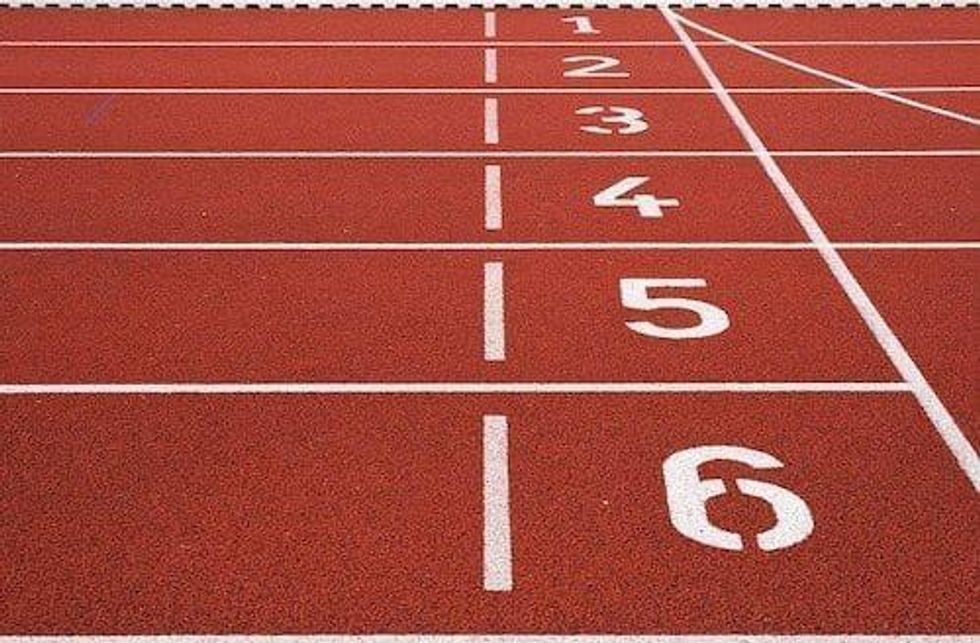
A look at North America’s EV battery megafactories plans, raw materials supply and what’s next for the region.
Electric vehicles (EVs) have become mainstream this past year, with sales in some regions increasing despite the COVID-19 pandemic, which put a pause on economies around the world.
As demand for EVs surges, the buildout of battery megafactories around the world is following suit as automakers and governments push for shorter supply chains and higher control.
China leads the way in megafactories, with Europe also taking sound steps to build these facilities, but North America has a long way to go to lead in this space.
Here the Investing News Network (INN) looks at North America’s EV battery megafactory plans, plus raw materials supply and what’s next for the region.
State of play in North America
North America’s EV industry is lagging behind other regions, even though Elon Musk’s Tesla (NASDAQ:TSLA) has been a pioneer in the US, providing high-end offerings for quite some time.
Speaking with INN about EVs in the US, Simon Schnurrer, partner and automotive expert at Oliver Wyman, said there are some segments in the US that are hard to push toward EVs, but original equipment manufacturers (OEMs) are planning for EVs in volume.
“It’s not just a high-end market for the rich, it should be a market accessible for everybody,” he explained. “This is a task that the industry is still working on — to make EVs less expensive and more attractive for a wider spectrum of customers.”
When looking at the entire EV supply chain for any region, taking ownership of every step seems to be equally important, but it is becoming increasingly clear that governments and automakers are moving to have further control upstream. To reduce costs and improve security, among other reasons, the buildout of battery megafactories around the world is picking up pace.
At present, Benchmark Mineral Intelligence is tracking 211 lithium-ion battery megafactories, but only 12 are in the US, while 156 are in China and 22 are in Europe. According to the firm, China is building a battery megafactory at the rate of one every week compared to the US at one every four months.
“While we have seen some considerable commitments from cell producers in the region, there is still a long way to go for it to become self-reliant for cells in the medium to long term,” Caspar Rawles, head of price assessment at the firm, told INN.
Benchmark Mineral Intelligence’s current forecast is for 410 GWh of capacity in North America by 2030.
“From Benchmark data, the region will need to see at least an additional US$30 billion to US$40 billion invested in cell production between now and then to meet regional demand,” he added.
Chart via Benchmark Mineral Intelligence.
North America has been moving slowly to supply its own battery needs, Kevin Shang of Roskill told INN, but the firm expects more battery megafactories to come.
Roskill forecasts that the US and Canada will occupy around 10 percent of global lithium-ion battery cell production capacity by 2030.
According to the firm’s research, 16 battery megafactories will be in operation in the US by 2030, far behind the number in China — but that is not to say the situation will remain the same.
“Automakers like GM (NYSE:GM), Ford (NYSE:F) and some startups have ramped up their electrification ambitions. Importantly, the (President Joe) Biden team has been moving very quickly,” Shang said.
In the short time since the new US administration took office, it has proposed an investment of US$174 billion in EVs, pledged for a new national goal to reduce carbon emissions by 50 percent by 2030 and called for more battery megafactories in the US.
“All of this would stimulate more battery megafactories to be built in the region,” Shang added.
Catching up to China and Europe
When asked about why the US has lagged behind China in the battery megafactory space, Shang highlighted that the automotive industry in the US has only recently started to embrace EVs, and the national policy was not in place to support the transition.
“By contrast, back in 2009, the Chinese government vowed to become a global leader in EVs,” Shang said.
Similarly, Rawles said it has largely been down to a lack of political impetus up until now.
“In China this has been a national priority for many years, and Europe acted more quickly than North America to bring in battery-related policies and subsidies,” he said.
However, the expert didn’t dismiss the possibility of North America catching up with Europe.
“I think a key lesson would be to share the focus across the value chain and not just on downstream cell and EV production,” Rawles said. “Raw material processing and cathode/anode production are fundamental to a healthy domestic lithium-ion economy, and this is something that needs to be ramped up in Europe.”
Roskill’s Shang was also optimistic about the opportunity that North America has going forward.
“Personally, I am positive that the US can catch up with Europe if regulation, investment and the industry work together effectively,” he said. “Back in 2017, there was little (in terms of) lithium-ion battery facilities in Europe. In the past three to four years, Europe has made impressive progress.”
Shang highlighted some key factors that have pushed Europe forward in this space, including strategic action and a unified strategy for batteries. Additionally, the EU is introducing a new batteries regulation with sustainability requirements for the whole lifecycle of EV batteries.
“This would make sustainability a competitive advantage for Europe’s batteries, compared with Asian products,” Shang said.
Another key factor that has helped Europe is its ability to attract public, private and industrial financing.
“The lithium-ion battery production capacity in the US is very Tesla-centric,” Shang said. “By contrast, the battery megafactories in Europe are more diverse, including East Asian battery makers, startups and auto-battery alliances.”
For his part, Schnurrer said there’s a good level of know-how in the EV space in the US.
“I would also like to think that at least the industrialization of the batteries and building the complete value chain will be a little bit smoother than Europe,” he said. “The US could learn some lessons that might help it spare some situations that we had in Europe, when due to non-availability of battery cells, vehicles couldn’t launch in time or couldn’t be sold in volume that they were planned for.”
However, for the expert, in terms of the role of the different players, the US will be different from Europe and will stay different from Europe. “The US, of course, has to find its own way, it cannot just copy paste mechanisms as they are in Europe,” he added.
Localizing supply chains in North America
Roskill believes that the American-made approach could become a challenge for the buildout and/or securing of raw materials and chemicals for battery megafactories in the near term.
“Although capital keeps flowing into the supply chain, the time gap between the investment and the completion of the facility, especially in mining and refining segments, which normally takes longer time, must be taken into consideration,” Shang said. “In addition, it takes several years, particularly for new entrants, to steadily produce high-quality materials to feed in EV battery manufacturing.”
Some parts of the North American supply chain have secured raw materials, but they are in the minority — those that haven’t will need to act quickly if they want secure supply, Rawles explained.
“We are starting to see longer contract terms in the battery supply chain, typically up to five years, but in some cases longer,” he said. “This means it is becoming increasingly difficult to enter into such agreements with tier one suppliers as less and less material is available.”
However, this is not a North America-only challenge. “It’s the same for the global supply chain, with the whole world vying for these critical minerals,” Rawles added.
Cathodes and anodes in North America
In 2020, North America only accounted for 1 percent of global cathode materials manufacturing capacity, according to Roskill data.
“We will see more cathode production in the region,” Shang said. “Localized production of cathode materials would play a key role in building a sustainable and domestic battery supply chain in North America, reducing the CO2 emissions caused by the materials transportation.”
For its part, Benchmark Mineral Intelligence assesses the buildout of cathode and anode capacity globally on a plant-by-plant basis, with capacity broken down into plants that are in operation, in construction and in planning.
“Even when taking all of these categories into account, North America only has enough pipeline capacity in the medium term to supply about 5 percent of its anode and cathode needs,” Rawles said. “We do anticipate more announcements on this front as cell capacity grows, but it highlights the disconnect between different parts of the supply chain.”
What about supply of raw materials?
High-nickel cathode chemistries, like nickel-cobalt-aluminum (NCA) and nickel-cobalt-manganese-aluminum, will be North American megafactories’ first choice, as they will be transferred to EVs with a longer range, said Shang.
That said, Roskill believes that the use of cathode chemistries will continue to be diversified.
“It is reported that General Motors and LG Chem (KRX:051910) are exploring to build the second US battery plant using a different, more cost-effective battery chemistry than nickel-based cathode, and Roskill thinks it is quite likely to be high-manganese cathode materials,” Shang said.
In addition, lithium-iron–phosphate (LFP) cathode chemistry will be a strong candidate in autonomous vehicles, the expert added.
“To date, the chemistry focus for cell plants in North America has been on medium- to high-nickel nickel-cobalt-manganese and NCA as the industry remains focused on extending range via more energy-dense cathodes,” Rawles said, adding that raw material demand will grow between seven and eight times over the next decade.
Key catalysts to watch
Looking ahead, one of the trends Rawles is expecting to see is a push for larger and more efficient facilities to assist with pushing down the cost of cells, as has been seen elsewhere. “We may also start to see some LFP capacity, but this would likely be some years away if it happens,” he added.
On the topic of reducing costs, Shang said battery megafactories are forecast to actively take part in upstream integration.
“This would allow them to gain a cost-competitive advantage by reducing battery manufacturing cost and controlling their supply chain to avoid price volatility in key raw material markets,” he said.
Additionally, Shang is expecting OEMs to participate in building battery megafactories, and forming joint ventures with battery manufacturers is a good starting point.
Another key trend to keep an eye on is the decarbonization of the supply chain — battery megafactories are expected to be built in areas with easy access to reliable supply of low-cost and renewable energy.
“At present, the US is lagging behind Europe in terms of legislative action (proposed or otherwise) to manage the sustainability profile of cathode manufacturing, but this is not to say this will remain the same,” Dominic Wells of Roskill told INN. “Sustainability of supply chains is going to become a much bigger issue in the battery manufacturing chain of the US over the next decade.”
Wells pointed to Biden’s pledge to reduce US CO2 emissions by 50 percent by 2030.
“A big contribution towards this will be the introduction of more centralized support for EV sales and battery manufacturing capacity,” he said. “In time, I would expect to see similar legislation be drafted governing the CO2 impact of the supply chains feeding this expected capacity, similar to how the EU is introducing its own schemes.”
Don’t forget to follow us @INN_Resource for real-time news updates!
Securities Disclosure: I, Priscila Barrera, hold no direct investment interest in any company mentioned in this article.
Editorial Disclosure: The Investing News Network does not guarantee the accuracy or thoroughness of the information reported in the interviews it conducts. The opinions expressed in these interviews do not reflect the opinions of the Investing News Network and do not constitute investment advice. All readers are encouraged to perform their own due diligence.