Recycling Key to Closing Supply/Demand Gap for EV Battery Materials
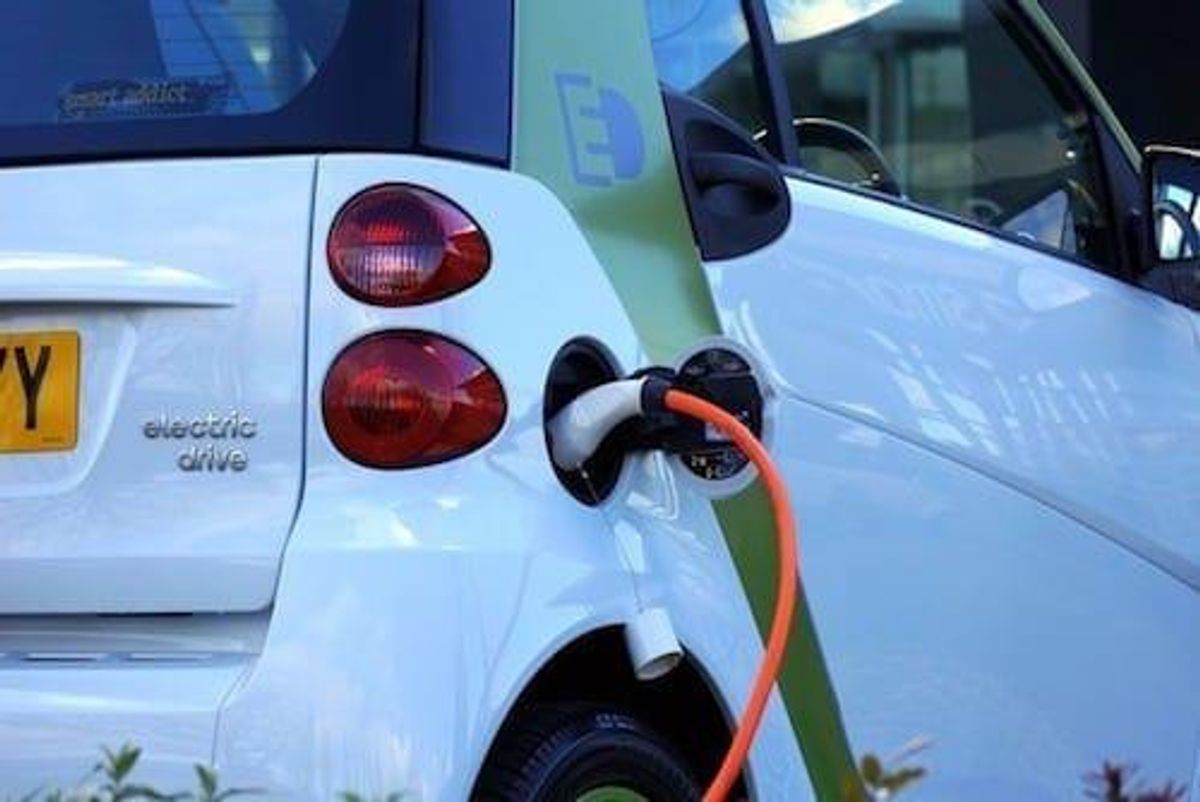
The electric vehicle industry’s need for lower-cost battery materials is reshaping battery recycling technology.
The global market share for electric car sales is expected to rise to 35 percent by 2030, up from less than 25 percent in previous forecasts, according to the International Energy Agency's 2023 Global EV Outlook Report.
However, the supply of electric battery materials can’t keep up with this exploding level of demand. Analysts say that EV production is pulling ahead of mine production for critical battery materials such as cobalt, manganese, lithium and nickel.
This is having a serious impact on prices. If the EV industry wants to overtake the internal combustion engine (ICE) sector, it will need to manage material prices by curbing supply imbalances. Advancement in battery recycling technology may be the answer.
EV battery costs need to fall further to overtake ICE
This expected growth of the EV market is driving demand for batteries and the critical metals associated with battery manufacturing. The International Energy Agency reports the demand for automotive lithium-ion batteries surged by approximately 65 percent to 550 GWh in 2022, up from around 330 GWh in 2021.
This increase is primarily attributed to a 55 rise in new electric passenger car registrations in the same period. Much of the growth in battery demand will come from China’s zero-emissions vehicle program. EV sales in China rose by 18 percent in the first three months of 2024, compared to the same period in the previous year. On a global scale, over one in four passenger cars sold will be an EV by 2030, according to a report by S&P Global.
This increased demand has only been made possible by the cost of EVs nearly reaching parity with that of ICEs. This equalization has been due in large part to lowering lithium-ion battery costs. More widespread adoption of the EV depends upon battery costs coming down even further.
Rising cobalt costs tied to supply crunch
A lower-cost lithium-ion battery requires lower cost materials. Today, the battery’s most expensive component is the cathode, and cobalt and nickel together account for about 80 percent of that cost. Cobalt prices in particular are at 10 year highs in light of rising demand for EV batteries coupled with supply constraints.
The EV battery industry currently consumes more than 40 percent of cobalt, according to the Cobalt Development Institute, and that figure could reach 65 percent or higher over the next decade. By 2030, EV batteries alone will account for 176,000 metric tons of cobalt demand worldwide.
A multi-year cobalt shortage is on the horizon, according to Macquarie Research, with continuing turmoil in the Democratic Republic of Congo (DRC) — which accounts for 65 percent of global cobalt supply. Technology producers such as Apple (NASDAQ:AAPL) are coming under fire to source conflict-free materials, but there are few sources of supply outside of the DRC.
The cobalt supply imbalance is causing battery manufacturers to look for more cost-effective chemical compositions that rely less on cobalt and more on nickel. However, such technology is years away and may not even be possible.
Nickel has its own supply woes
Further complicating the cost scheme for EV batteries, nickel comes with a similar supply problem. Battery manufacturers need nickel sulfate powder derived from high-grade nickel sulfide deposits for which there are few in production and not many are currently even under exploration or development.
“The problem for the nickel industry is it’s not a macro issue; it’s not an issue where we’re going to run out of nickel, but the specific nickel that’s required,” Jon Hykawy, president of Stormcrow Capital, told the Investing News Network at the 6th International Nickel Conference. “The specific chemistry and the specific purity that’s required for batteries is likely going to put a strain on the supply chain.” Iasnikov sees this looming supply crunch as the demand for nickel sulfate rises an estimated 138.6 percent from current levels to reach 167,000 tpy by 2025.
In order for EV sales to overtake the market from fossil-fuel-powered vehicles, the industry will have to find a sustainable way to get prices for critical materials like cobalt and nickel under control. Battery recycling is one of the proposals being put forward to curb the supply imbalance on the horizon.
Battery recycling key to managing cost dynamic
Battery recycling may soon become a more cost-effective source of materials compared with the cost of mining new materials. More cost reductions can be made by recycling materials like cobalt and nickel directly from spent batteries onsite at battery manufacturing facilities. Recycled cathode metals would also have a much smaller footprint than a traditional mining operation. “Spent lithium-ion batteries are considered hazardous waste, so it is highly expensive to ship spent batteries. Having smaller localized recycling plants would be more cost effective,” Norman Chow, founder and president of Kemetco Research, one of the Canada’s largest private contract R&D firms, told the Investing News Network.
Kemetco has worked with RecycLiCo Battery Materials (TSXV:AMY,OTCQB:AMYZF,FWB:2AM) to develop the company's commercialized and scalable recycling technology for the lithium-ion battery industry. The patented technology is a hydrometallurgical process that involves a complete closed-loop flowsheet developed to maximize metal recovery while minimizing reagent usage and recycling water.
During laboratory-scale testing, Kemetco and RecycLiCo successfully recovered 100 percent of the lithium, cobalt, nickel, manganese and aluminum materials by recycling cathode materials in the four most widely used cathode compositions, including lithium-cobalt-oxide (LCO), lithium-manganese-oxide (LMO), nickel-manganese-cobalt (NMC) and nickel-cobalt-aluminum (NCA) batteries. More importantly, the technology was able to reformulate all four of these cathode chemistries from the recycled materials.
Current battery recycling infrastructure insufficient to tackle the challenge
Today, there are only a handful of companies that have the technology and capacity to recycle cathode materials from lithium-ion batteries. The issue of capacity is one of the major challenges to battery recycling becoming a viable source for future EV battery materials, but one that can be addressed. “Recycling is difficult for the battery industry, but this is the only way to keep nickel and cobalt at a reasonable amount where the industry can afford to buy,” said Iasnikov.
There is no known commercial technology for the large-scale recycling of cathode materials of multiple chemistries. “There still needs to be more development to get to closed-loop recycling where all materials are reclaimed,” said Jessica Alsford, who leads Morgan Stanley’s (NYSE:MS) global sustainable research team.
Tesla has said it will recycle its own batteries in house. China and the EU have mandated that car makers be responsible for recycling the lithium-ion batteries in the EVs that come off their assembly lines. China, for example, is implementing recycling programs whereby car manufacturers are responsible for collecting and recycling EV lithium-ion batteries. EU regulations also require battery manufacturers to pay for recycling batteries past their prime, and these companies are beginning to partner with recyclers.
Such legislation may push the industry to look for more efficient and cost-effective battery recycling technology than the current shredding or smelting methods, which are highly inefficient and far from economical.
This INNSpired article was written as part of an advertising campaign for a company that is no longer a client of INN. This INNSpired article provides information which was sourced by INN, written according to INN's editorial standards, in order to help investors learn more about the company. The company’s campaign fees paid for INN to create and update this INNSpired article. INN does not provide investment advice and the information on this profile should not be considered a recommendation to buy or sell any security. INN does not endorse or recommend the business, products, services or securities of any company profiled. If your company would benefit from being associated with INN's trusted news and education for investors, please contact us.