Retooling Technologies to Aid South African Platinum Production
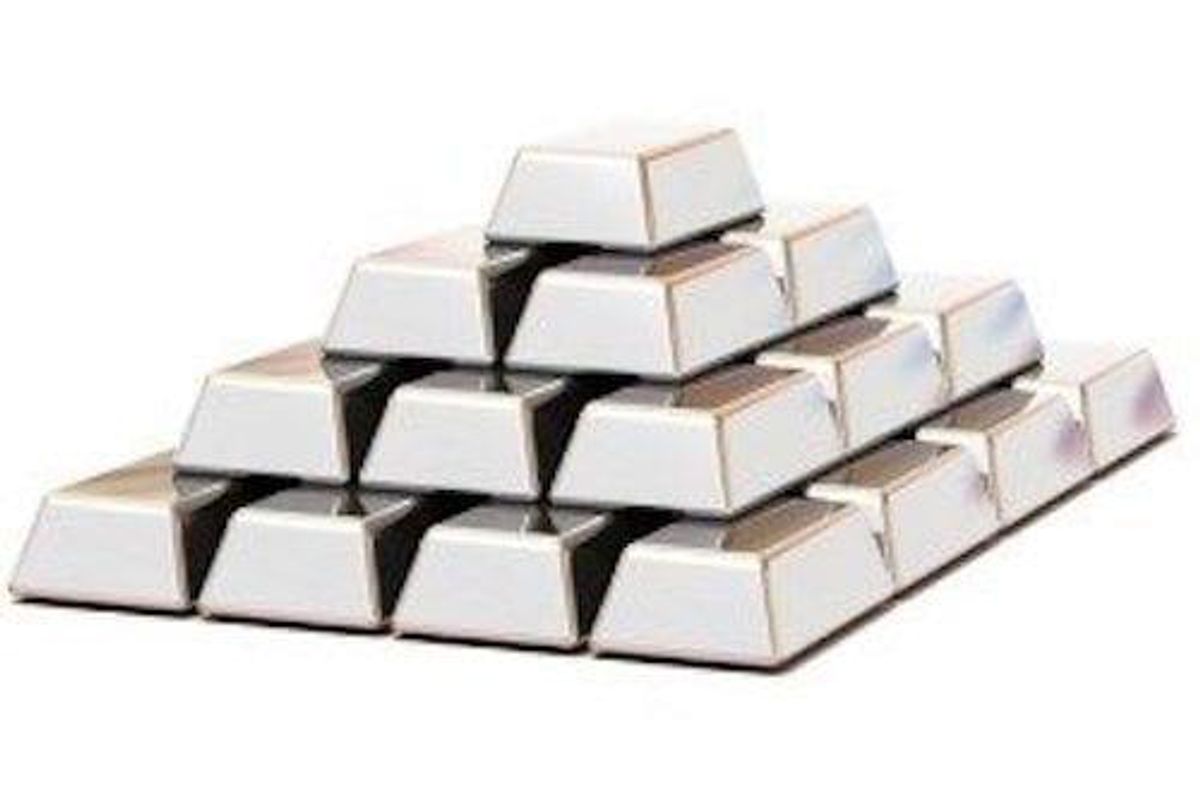
Innovations that are typically reserved for subways and landmines are now being reconstructed for use in South African platinum mines.
Technologies currently used to carve subways and clear landmines are being reconstructed for use in South Africa. The move could help the country’s platinum mines become more profitable and provide a lifeline for some loss-making shafts.
The sector has been battling low prices as well as social unrest for some time, with only a handful of South Africa’s platinum shafts making money; the majority run a deficit.
“Under current price and cost forecasts, conventional [platinum] mining ceases to be economically viable in 2024,” stated South Africa’s Chamber of Mines.
The updated technologies include a 60-centimeter-high bulldozer built by Croatian landmine clearance company Dok-ing. The South African platinum reef is usually too steep and narrow for machines to access, so Dok-ing began by building compact dozers that clear landmines and sweep away ore.
The dozers’ tank-like treads help to resolve a key mechanization challenge, which is the inability of machines with traditional tires to mine steep gradients. Additionally, Dok-ing’s dozer design enables the machines to work on reefs at gradients of up to 22 degrees and beyond.
“Most machines … cannot work above 14 degrees because their wheels simply cannot generate power at such steep gradients,” said Declan Vogt, a lecturer in mining automation at Britain’s University of Exeter.
Anglo American Platinum (JSE:AMS) subsidiary Implats plans to use the technology to boost the profitability of shafts at its Amandelbult mine, and Lonmin (LSE:LMI) CEO Ben Magara has said his company is already using three of the dozers at its Saffy shaft.
Despite positive results from the retooled tech, costs are still a concern for South African miners. “The up-front capital is the challenge and given the constraints in the industry, that is not small,” Magara said.
Johan Theron of Impala Platinum (JSE:IMP) added, “it is a complicated process to switch to mechanization. You need to cut jobs, bring in new skilled workers, set up workshops, and make other adjustments.”
The second innovation that could help South Africa’s platinum industry involves dispensing with blasting. This allows for undisrupted work as it eliminates the task of clearing mines for detonations.
The Rapid Mine Development System, designed by Atlas Copcounit Epiroc, works as it churns the rock face with a steel disk. This type of technology has been used in coal mines for decades, but this is the first time it has been used in a hard-rock platinum mine.
By incorporating this innovation, mines are smoother, with only grooves left — much like a subway, for which the technology was originally designed.
Platinum miners are now beginning to see that mechanizing is important if they want to survive. “If you look at the bottom end of the cost curve, it is dominated by mechanized mines. Machines do the heavy lifting so productivity is significantly different,” said Northam Platinum (JSE:NHM) CEO Paul Dunne.
Northam has mechanized its Booysendal mine, which is currently is ramping up production.
As for Implats, its annual results show that its Rustenburg operation, which uses traditional technology, last made a profit in 2014 and has since lost around US$1.12 billion. By contrast, mechanized Two Rivers is Implats’ lowest-cost operation.
Don’t forget to follow us @INN_Resource for real-time news updates!
Securities Disclosure: I, Nicole Rashotte, hold no direct investment interest in any company mentioned in this article.