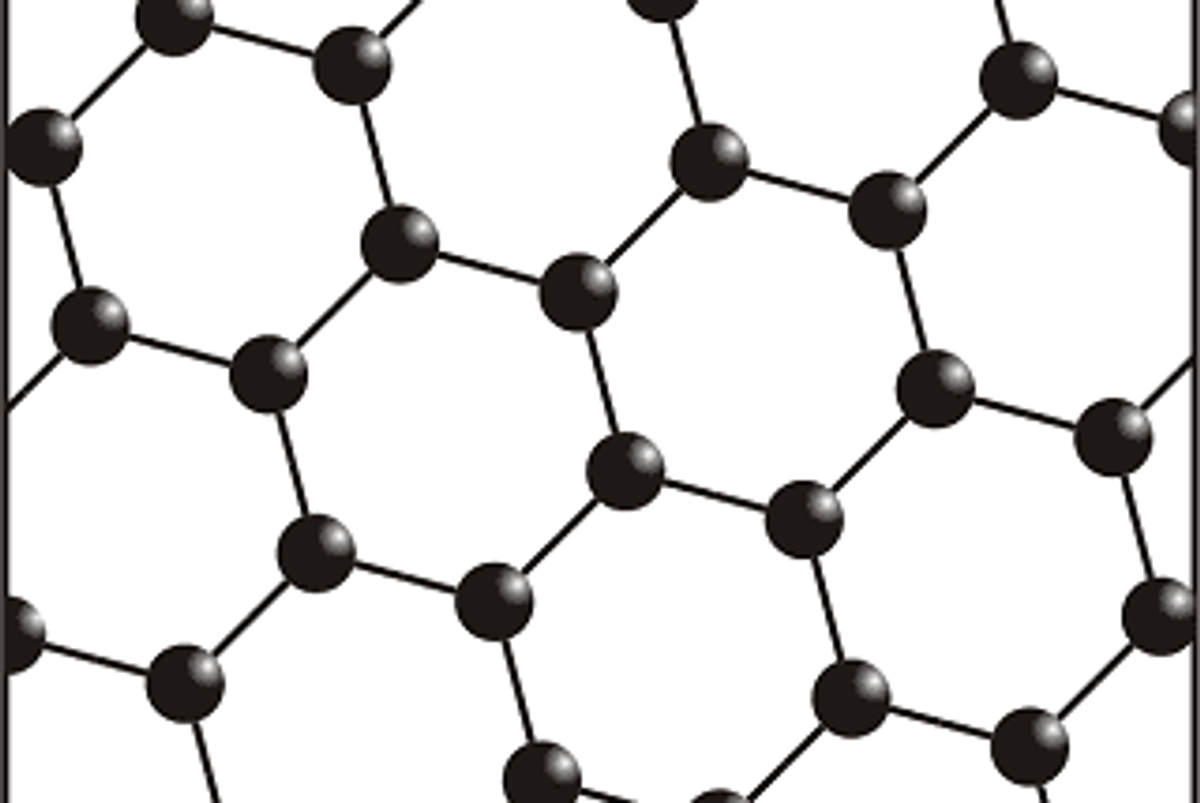
Graphene’s market opportunities are starting to arrive.
By Simon Rees
This article was originally published in Benchmark Mineral Intelligence‘s December 2015 magazine. Click here to view the full magazine in PDF, or click here to view it on Tablish.
At the 1855 Exposition Universelle in Paris a wondrous new metal wowed the crowds: aluminium. The enthusiasm surrounding it belied the decades of research taken to reach that point, with the big breakthrough occurring when Henri-Etienne Sainte-Claire Deville started producing the material on a commercial scale.
However, aluminium proved phenomenally expensive; France’s Emperor Napoleon III is said to have honoured special dinner guests by providing them with aluminium cutlery. Everyone else had to make do with gold or silver.
The price only fell with the development of the Hall-Heroult process and cheaper energy later in the century. Aluminium had been struggling to win market share until that point. “There is nothing harder than to make people use a new metal,” Sainte-Claire Deville once rued.
Some of aluminium’s early difficulties might be familiar for those working with graphene. Many thousands of hours have been spent studying the material over the past decade, with an avalanche of related patents testimony to this.
There is also debate about how scale-up production, make the material affordable and find the right first-entry markets – similar conundrums aluminium faced all those years ago.
On your marks
Source: The University of Manchester.
Graphene’s recent history only stretches back to 2004 when Andre Geim and Kostya Novoselov famously used Scotch tape to lift graphite from a sample. They then repeatedly folded and unfolded the tape to isolate the graphene.
It comprises just one element, carbon, and has superb strength; it is more than 200 times stronger than steel by weight. Graphene is transparent, with a hexagonal, honeycomb-like formation at a layer just one atom thick.
It is also light-weight, stretchable and flexible. In addition, it is a semimetal and can take on magnetic qualities. It impermeable and is the best thermal and electrical conductor yet known. Cambridge University and others have been working on copper wiring that utilises graphene.
“That’s a possible early-stage market,” Tata Steel principal scientist Siva Bohn told Benchmark Mineral Intelligence (Benchmark). However, there is little room for impurities. “When you have impurities, even just 5%, then conductivity goes down the drain.”
At an industrial level it would require high-quality graphene produced in quantity. Unfortunately, scaled-up production is where graphene faces some of its greatest hurdles. There are “top-down” and “bottomup” methods to make graphene. Top-down includes exfoliation, the splitting of graphite down to microlayers of graphene and the Scotch tape method is a rudimentary version of this.
Electrochemical treatments can also be used. For example, graphite-in-solution bombarded with ultrasound to create flakes of graphene that can be further processed in a centrifuge.
Bottom-up methods include chemical synthesis or gas-phase growth. For example, chemical vapour deposition uses a substrate placed in a furnace through which methane and hydrogen gases are passed. The carbon atoms within the methane then fall to the substrate and form a graphene layer.
There is some debate about how many layers constitute graphene. Bohn noted that a bi-layer or tri-layer can be considered graphene. “And some people call as many as 10 or 20 layers graphene.”
Because of its conductivity, graphene could be integral to produce superfast transistors for computers or electronic devices. It is also chemically inert, which means it can be readily used alongside other materials.
That can be important for electronics doping purposes, whereby another material is introduced alongside the graphene to modulate performance. This would allow manufacturers to “dumb down” graphene’s conductive properties for other electronics components to remain optimal while raising overall performance.
There are a plethora of other attributes and potential uses, most notably in the batteries space, where graphene’s conductive and impermeable qualities could be readily utilised. However, the development and roll-out of this technology remains some way off.
It takes time for markets to adapt and realise a new material’s full potential. “New technologies based on new materials take from between 20 and 40 years to go from the lab to the factory floor,” Cambridge University professor of Nanotechnology Andrea Ferrari noted in a recent presentation.
New materials moving beyond pilot production usually seek out the easiest, most accessible entry points in a marketplace first. Often this is as a displacement material for improving the performance of existing technology. For example, graphene is already used in top-quality sporting equipment, such as Novak Djokovic’s lightened and strengthened tennis racquets.
Lick of paint
Perth-headquartered Talga Resources is advancing its flagship Vittangi graphite project in northern Sweden. The company seeks to tap graphene’s potential within paints and protective coatings and it signed a collaboration agreement with Tata Steel UK on November 9 to jointly explore graphene opportunities in supply, processing and development.
Paint and coatings are expected to have the benefit of robust margins and uptake, Talga Resources MD Mark Thompson told Benchmark. The company notes the market currently uses over 40 million tonnes of material a year, which is forecast to grow to 52 million tonnes by 2017 and have a value of $186 billion.
Graphene would be infused within the paint or coating to confer its impermeable qualities, helping to block water, liquids or other corrosive elements reaching the metal beneath. Ensuring graphene’s even dispersal in the product will be vital for these strengths to come into play.
However, not much graphene is needed in terms of its loading within the paint, Thompson said. “Zinc oxide paint comprises something like 90% zinc. With graphene it’s around 1% that can be diffused for it to have an amazing effect.”
“Let’s say graphene costs $50,000 per tonne, which some might think expensive,”he continued. “Well the paint costs roughly $50,000 per tonne, but only 1% of it will be graphene. That means a total graphene cost of just $500 dollars on a production basis because 1% of $50,000 is just $500.”
There are health and safety advantages as well. For example, hexavalent chromium used to make chrome coating has toxic properties and has already been banned or is about to be banned in many jurisdictions.
Source: Tata Group.
“So here you’d be replacing something toxic with a non-toxic carbon [i.e. graphene],” Thompson said. “And that fits the pattern whereby it’s not always necessary for something to outperform what it replaces if it’s the healthier, environmentally-friendly option.”
Graphene-infused anti-corrosive paints and coatings could also prove particularly important for vehicles, increasing protection against the threat of corrosion and prolonging vehicle life through this.
In addition, there is the added benefit of requiring fewer layers of anti-corrosive paints and coatings. That could deliver weight savings and improve fuel efficiencies as a result.
The use of graphene to impart mechanical strength and stiffness to components will be another important application for the future and it will also help to reduce weight and achieve fuel savings. “But that technology will take a few years,” Bohn noted.
Electric dreams
While anti-corrosive paint and coatings are likely to be one of the first entry-level markets for graphene, the topic is unlikely to fire the general public’s imagination. That role is currently being fulfilled by graphene’s near-term potential in touchscreens and light-sensitive technology.
“Taking the broad perspective, I think electronic devices could be the place we see the breakthrough in technology with graphene,” Michigan University head of the Zhong Group Professor Zhaohui Zhong told Benchmark. The Zhong group focuses on Nanoelectronics and Nanophotonics.
“[Graphene] has strong light absorption all the way from ultraviolet to infrared – it’s a super-absorbent absorption material as it were,” he said. “In addition, it’s really unlike any other semiconductor where the absorption is typically limited and there’s an energy gap, called a band gap.”
Transparent graphene can be layered over plastic to create touchscreens and provide the same if not a better experience for tablet, laptop or smartphone users. “This will be the low-hanging fruit,” Zhong added.
Current touchscreens can be easily scratched and often cracked, while graphene, with its strength and flexibility, could afford far better protection.
Today’s touchscreen technology also utilises indium tin oxide. Indium is not a readily-available material and is expensive because of this. By contrast, the sources for making graphene are plentiful, which also guarantees supply for end users.
Further into the future there is the possibility of “bendy” phones and tablets that can be rolled up or folded and the mainstream media has excitedly depicted this potential aspect of graphene’s story with mock-up images or graphics.
However, a great deal of design work will be required to make something like the bendy phone feasible. For example, what kind of battery will be used and where will it be positioned? Does the device use USB connection points or will they be done away with?
Predicting the development of a material is difficult, predicting its future applications in technology yet to come is harder still. However, it is certain graphene will perform as expected in many areas and falter or fail in others. Undoubtedly it will also make new technologies possible.
But even as a displacement material for established technologies, such as anticorrosive paints and coatings, graphene is already on the cusp of becoming an integral, even ubiquitous, part of our lives.