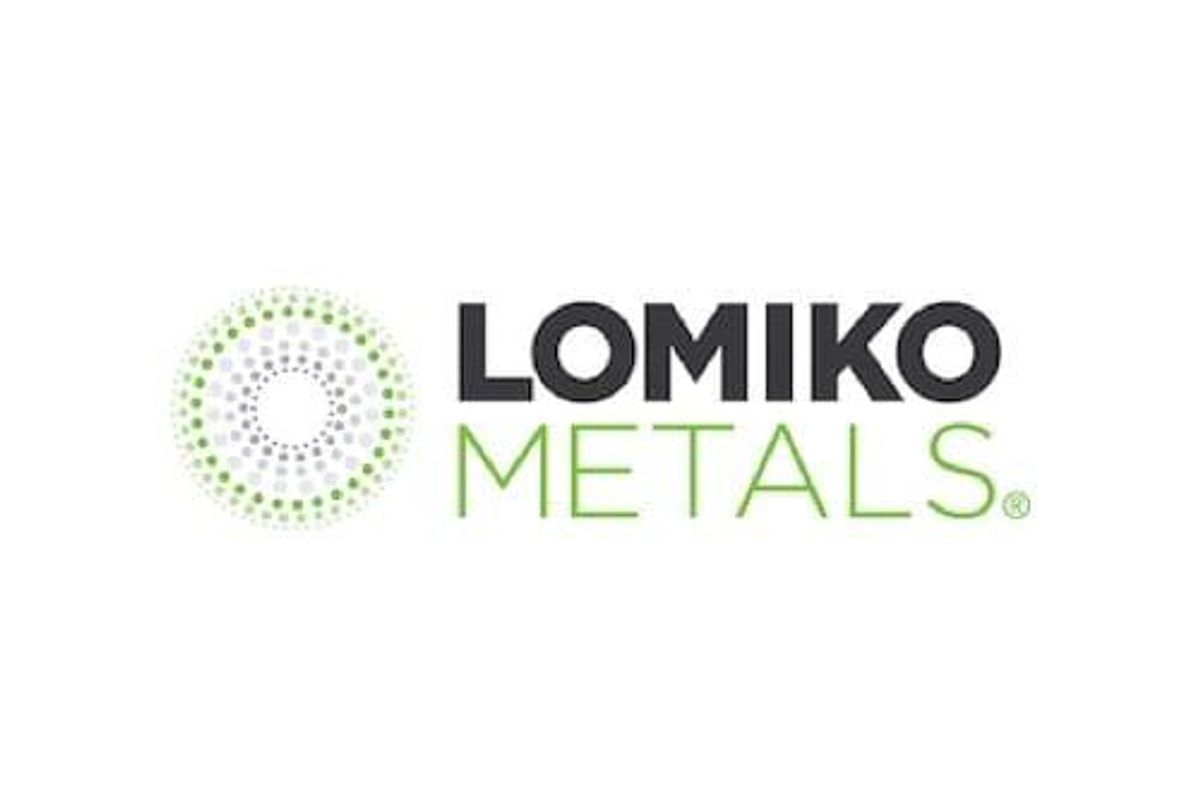
Lomiko Metals Inc. (TSX-V: LMR, OTC: LMRMF, FSE: DH8C) (Lomiko or the "Company") is pleased to provide an update on its La Loutre graphite project ("La Loutre"), located in Quebec, Canada. La Loutre comprises the Graphene-Battery (GB) zone and the Electric Vehicle (EV) Zone. The names of the zones are not reflective of the products each will produce but generally indicate applications of products. The recent testwork program confirmed that each zone will produce similar products.
This press release features multimedia. View the full release here: https://www.businesswire.com/news/home/20210407005392/en/
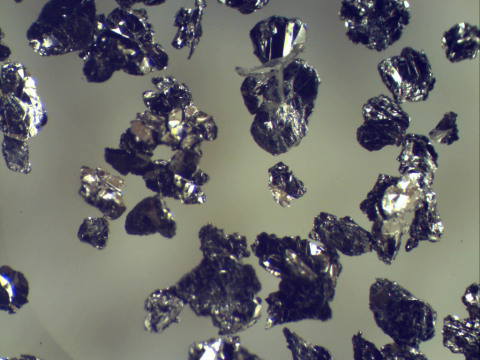
Quebec Crystalline Flake Graphite (Photo: Business Wire)
Highlights
- A metallurgical flowsheet development program was carried out on two composite samples of La Loutre graphite project. One composite was generated from mineralized samples from the EV zone yielding 9.70% graphitic carbon, and the second composite from drill core of the GB zone yielding 4.80% graphitic carbon.
- The process development was carried out on both composites and resulted in a flowsheet and conditions that are suitable to treat both zones of La Loutre mineralization in the same processing plant.
- The program culminated in a locked cycle test ("LCT") that generated a combined concentrate grading 97.8% total carbon at 93.5% graphite recovery.
- Although the two mineralized zones produced noticeably different flake size distributions, they responded equally well to the same flowsheet and conditions with combined concentrate grades of over 97% total carbon.
"These very encouraging results of initial testing suggest that La Loutre graphite may be suitable for high-end industrial use," stated A. Paul Gill, CEO. "Our next step is to complete a Preliminary Economic Assessment."
Technical Discussion
Process Development
In January 2021, a metallurgical process development program was initiated at SGS Minerals in Lakefield, Ontario. The objective of the program was to develop the flowsheet and conditions suitable to upgrade La Loutre mineralization to at least 95% total carbon.
Metallurgical development work was carried out on two composites representing the two zones. The process development program produced a flowsheet and conditions that generated concentrates of over 97% total carbon for both mineralized zones. The equipment and reagents selected for the process are well established in the mineral processing field and are consistent with other graphite projects. The flowsheet, which is depicted in Figure 1, comprises rougher/scavenger flotation stage, followed by a primary and secondary cleaning circuit.
The GB composite produced a final concentrate with a significantly higher mass recovery into the +80 mesh size fraction of approximately 50% compared to 25-30% for the EV composite. However, both composites responded equally well to the same flowsheet and conditions, producing combined concentrate grades that are consistently at least 97% C(t).
The program culminated in a locked cycle test (LCT) using a 50:50 blend of the two mineralized zones. The overall mass balance is presented in Table 1. The mill feed grading 7.60% carbon was upgraded to a combined concentrate grading 98.5% carbon at an overall graphite recovery of 93.5%.
Table 1: Mass Balance of Locked Cycle Test LCT-1
Sample ID | Weight | Assays (%) | % Distribution | ||
% | C(t) | C(t) | |||
Combined Concentrate | 7.2 | 98.5 | 93.5 | ||
+80 Mesh 2nd Clnr Conc | 2.9 | 99.0 | 37.1 | ||
+80 mesh 1st Clnr Tails | 0.1 | 34.9 | 0.3 | ||
-80 mesh 3rd Clnr Conc | 4.4 | 98.1 | 56.4 | ||
-80 mesh 1st Clnr Conc | 0.4 | 9.64 | 0.5 | ||
1st Clnr Tails | 22.3 | 1.26 | 3.7 | ||
Scav Tails | 69.9 | 0.21 | 1.9 | ||
Head (calc) | 100.0 | 7.63 | 100.0 |
The final concentrates of the three cycles that were used to develop the overall mass balance were submitted for a size fraction analysis (SFA), and the average results of the three SFAs are presented in Table 2. The combined concentrate grade of 97.8% total carbon is slightly lower compared to the direct concentrate analysis of the LCT mass balance, which is related to measurement uncertainties associated with assay methods.
A total of 32.4% of the concentrate mass reported to the +80 mesh size fractions at a combined grade of 97.8% total carbon. Another 10.8% of the mass was recovered into the -80/+100 mesh product at a grade of 98.2% and the balance of 56.8% reported to the -100 mesh size fractions at a combined grade 97.7% total carbon.
One of the primary applications for the -100 mesh size fraction is the value-add process to produce spherical graphite for batteries. The ability to upgrade the fines size fraction to almost 98% total carbon by flotation only might have a positive impact on downstream purification costs since concentrations of impurities are often proportional to purification cost.
Table 2: Average Size Fraction Analysis Results of LCT-1
Size | Mass | Grade | Distribution | ||
Mesh | Microns | % | %Ct | %Ct | |
|
|
|
|
| |
32 | 500 | 1.0 | 97.6 | 1.0 | |
48 | 300 | 9.8 | 97.4 | 9.7 | |
80 | 180 | 21.6 | 98.0 | 21.7 | |
100 | 150 | 10.8 | 98.2 | 10.9 | |
150 | 106 | 17.5 | 98.1 | 17.5 | |
200 | 75 | 13.0 | 98.3 | 13.1 | |
325 | 45 | 13.5 | 98.1 | 13.6 | |
Pan | -45 | 12.8 | 96.0 | 12.5 | |
|
|
|
|
| |
Total |
| 100.0 | 97.8 | 100.0 |
Preliminary comminution tests produced Bond ball mill work indices of 6.9 kWh/t for the EV zone and 11.2 kWh/t for the GB zone, which places La Loutre mineralization into the very soft to soft category, which is favourable for minimizing grinding energy costs.
Next Steps
Variability flotation testing on four composites that made up the two development composites will be performed to complete the scoping level metallurgical study.
The combined concentrate of the LCT will be subjected to chemical and mineralogical characterization, which will determine the type and association of the remaining impurities in the graphite concentrate. This information will be used to commence marketing initiatives for La Loutre graphite concentrate.
The current process development program will be completed within the next couple of weeks, and the company commenced work on a preliminary economic assessment (PEA) study.
During the next phase of metallurgical testing, conditions of the existing flowsheet will be optimized to minimize flake degradation and maximize graphite recovery. Further, the optimization will evaluate potential capital and operating cost savings.
The robustness of the optimized flowsheet and conditions will be verified with a larger number of variability samples, and a more comprehensive comminution program will be completed.
Qualified Persons
Mr. Oliver Peters, a Principal Metallurgist with Metpro Management Inc., is a Qualified Person within the meaning of NI 43-101. Mr. Peters is satisfied that the analytical and testing procedures used are standard industry operating procedures and methodologies, and he has reviewed, approved and verified the technical information disclosed in this news release, including sampling, analytical and test data underlying the technical information.
Quebec's Role in The New Green Economy
In 2020, The Quebec Government released the Quebec Plan for Development of Critical and Strategic Minerals ("The Quebec Plan") which indicates graphite demand would likely increase 300-500% in the coming decades as more is used in the production of spherical graphite for anode portion of Electric Vehicle Lithium-ion batteries. Quebec has an opportunity to play a vital role in reducing carbon emissions and become a key provider of critical battery materials to the North American economy.
For more information on Lomiko Metals, review the website at www.lomiko.com , contact A. Paul Gill at 604-729-5312 or email: info@lomiko.com .
On Behalf of the Board,
"A. Paul Gill"
Chief Executive Officer
We Seek Safe Harbour. Neither TSX Venture Exchange nor its Regulation Services Provider (as that term is defined in the policies of the TSX Venture Exchange) accepts responsibility for the adequacy or accuracy of this release.
View source version on businesswire.com: https://www.businesswire.com/news/home/20210407005392/en/
A. Paul Gill
604-729-5312
info@lomiko.com