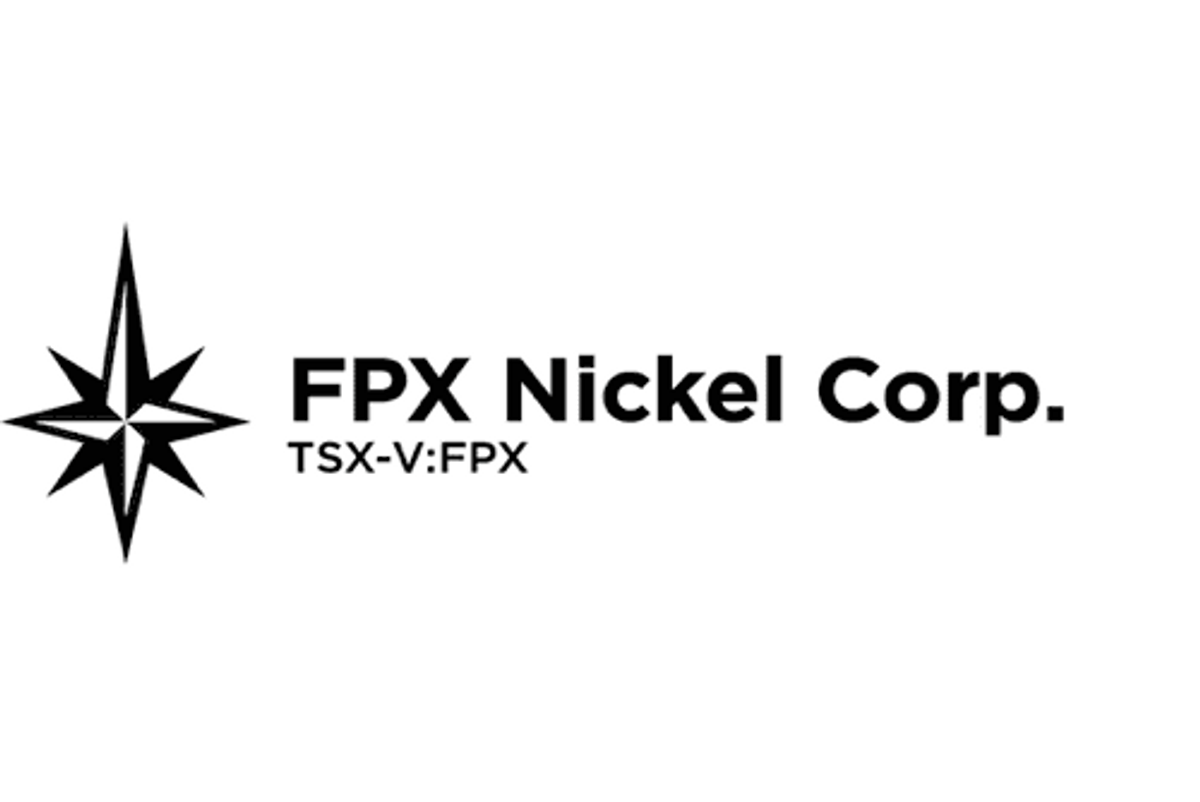
 
 FPX Nickel Corp. (TSXV: FPX) (OTCQB: FPOCF) (" FPX " or the " Company ") is pleased to present results from recently completed large-scale pilot testwork, with results validating both the flowsheet and the 85% Davis Tube Recoverable (" DTR ") nickel recovery assumed in the 2020 Preliminary Economic Assessment (" 2020 PEA ") for the Baptiste Nickel Project (" Baptiste " or the " Project ") at the Decar Nickel District in central British Columbia. The Company's current large-scale, three-phase metallurgical testwork program, which has been ongoing since mid-2021, will conclude in the second quarter of 2023 and the resulting dataset will support the completion of the Baptiste Preliminary Feasibility Study (" PFS ").
ÂÂ Highlights Â
 - Large-scale pilot testwork is now complete and sufficient high-grade (> 65% nickel) awaruite concentrate was produced for downstream hydrometallurgical testing for the production of battery-grade nickel sulphate Â
- Large-scale pilot testwork validates the processing strategy for Baptiste, leveraging awaruite's ferromagnetism, high density, active surface properties, and very high nickel content into a simple flowsheet utilizing magnetic separation followed by conventional froth flotation Â
- Consistent with the PEA, the PFS metallurgical testwork program confirms a minimum 85% DTR nickel recovery basis for the Baptiste PFS, including: Â
- Pilot-scale magnetic separation and bench-scale flotation testwork confirm an overall minimum DTR nickel recovery of 82% to a high-grade awaruite concentrate Â
- Bench-scale testwork confirms the potential to improve DTR nickel recovery by an additional 3-5% through atmospheric leaching of flotation tailings followed by hydroxide precipitation Â
"Our current three-phase metallurgical testwork program confirms earlier results that demonstrate the technical feasibility of the Baptiste Nickel Project," commented Andrew Osterloh , FPX Nickel's Vice-President, Projects. "Large-scale pilot testwork is an effective tool for the Company to validate our straightforward processing strategy, which is based on awaruite's unique characteristics, leading to a simple concentrator flowsheet with a robust recovery basis. As we continue to demonstrate Baptiste's ability to produce very high-grade nickel concentrates, we further confirm that Baptiste's concentrate does not require intermediate smelting before use in either the stainless steel or electric vehicle battery supply chains, which is an important value differentiator for the Project."
ÂÂ Summary Â
 The Baptiste processing strategy leverages awaruite's distinct properties in a simple, yet robust flowsheet. The front end of the flowsheet utilizes magnetic separation to create a "magnetics rich" concentrate of awaruite and magnetite – a process made effective due to awaruite's ferromagnetism and density. The back end of the flowsheet then utilizes conventional froth flotation to separate awaruite from magnetite – a process made effective due to awaruite's active surface properties and magnetite's general lack of flotability. Finally, based on awaruite's very high nickel content, a very high-grade nickel concentrate (50-65% nickel) can be produced. Figure 1 presents the Baptiste flowsheet and Table 2 in the following section presents further details on Baptiste's processing strategy. As noted in Figure 1, a new processing opportunity treating flotation tailings has been identified, and the results are discussed herein.
ÂÂ
   Â
The Company's three-phase metallurgical testwork program, which has been ongoing since mid-2021, is approximately 85% complete and will conclude in the second quarter of 2023. The program includes both bench- and pilot-scale testwork and evaluates the comminution, magnetic separation, flotation, and hydrometallurgical unit operations. The overall program will test approximately 25 tonnes of material, including a life-of-mine master composite, mine phase composites, and a bulk sample from the starter pit area. Key results from the PFS metallurgical testwork program are presented in Table 1.
 Table 1 – Key PFS Metallurgical Testwork Program Results – DTR Ni Recovery Â
ÂÂ
Â
    DTR Nickel Recovery    |     PEA Criteria    |     Preliminary PFS Criteria    |  |
  Stage |    Primary Magnetic Separation   |    90 %   |    94 %   | Â
  Cleaner Magnetic Separation   |    100 %   |    99 %   |  |
  Flotation   |    94 %   |    88 %   |  |
  Overall Recovery   |    85 %   |    82 %   |  |
  New Opportunity – Flotation Tails Leaching   |    -   |    3-5% improvement; leading to | Â
Â
ÂNote that Table 1 presents a preliminary view on PFS recovery criteria, and that the in-progress variability testwork (see Table 3 in the following section) will confirm final PFS recovery criteria. As noted in Table 1, primary magnetic separation stage recovery has improved versus the 2020 PEA, balancing the effect of reduced flotation stage recovery versus the 2020 PEA. Additionally, flotation tailings nickel leaching represents a significant new opportunity to improve overall nickel recovery to match or exceed the 85% recovery assumed in the 2020 PEA.
ÂÂ Background Â
 The Company has completed approximately 85% of a three-phase PFS metallurgical test program aimed at validating the Baptiste processing strategy, flowsheet, and key process parameters.  The Baptiste processing strategy leverages awaruite's unique characteristics and is summarized in Table 2.  The overall program is summarized in Table 3, resulting in a robust dataset to support the Baptiste PFS. Phase 3 of the program has been subdivided into three components, as identified in Table 3.
 Table 2 – Awaruite's Distinct Properties and Baptiste's Processing Strategy Â
ÂÂ
Â
    Awaruite Property    |     Value    |     Processing Strategy to Leverage Property    | Â
  Ferromagnetic   |    Highly ferromagnetic; |    Use low intensity magnetic separation to cleanly | Â
  Very Dense   |    Specific gravity of 8.6;  Â compared to the serpentine gangue |    Select a coarse primary grind size while maintaining | Â
  Active Surface Properties   |    Comparable to sulphide minerals   |    Use froth flotation to cleanly separate awaruite | Â
  Very High Nickel Content   |    77% nickel  Â (Ni 3 Fe)   |    Produce a mineral concentrate by froth flotation that | Â
Â
 Table 3 – Summary of Three-Phase PFS Metallurgical Testwork Program Â
ÂÂ
Â
    Phase    |     Objective    |     Key Results    |     Status    | Â
   1    |    1. Confirm PEA magnetic separation  2. Expand comminution and grinding |    1. PEA magnetic separation  2. Generation of a PFS-level |    Complete  Â Â Refer to FPX | Â
   2    |    1. Confirm nickel mineralogy across  2. Confirm PEA conclusion that froth |    1. Consistent mineralization confirmed  2. PEA froth flotation configuration and |    Complete  Â Â Refer to FPX  July 27 th , 2022   | Â
   3a    |    1. Large-scale, longer duration pilot  2. Generate sufficient high-grade |    1. Further validation of PEA flowsheet  2. Sufficient high-grade concentrate |    Complete  Â Â Refer to this | Â
   3b    |    Variability testing to confirm the |    Testing in progress   |    Results forecast | Â
   3c    |    Hydrometallurgy testing program to |    Testing in progress   |    Results forecast | Â
Â
ÂThe overall metallurgical testwork campaign is being overseen by Jeffrey B. Austin , P.Eng., President of International Metallurgical and Environmental Inc.
 Phase 3a –Large-Scale Pilot Testwork Â
 Building on Phase 1 piloting, the Company undertook large-scale pilot testwork to (1) further demonstrate the recovery benefits of plant-scale processing, and (2) generate sufficient high-grade awaruite concentrate for hydrometallurgical testing. The Company engaged Corem ( Quebec, Canada ) to conduct this testwork based on their expertise in magnetic separation and conventional froth flotation and their extensive, world-class facilities. FPX's metallurgical team worked closely with Corem to optimize a wide range of parameters for each unit operation in the flowsheet, which was only possible due to the large overall scale of the pilot testwork.
ÂInitial results of the large-scale pilot testwork were reported in the Phase 2 news release ( July 27, 2022 ) and focused on the performance of the primary grind and magnetic separation unit operations. Â This release provides complete results from the large-scale pilot testwork, which is now substantially complete.
Â17 tonnes of material were processed in the pilot test conducted at Corem. The feedstock for piloting was a bulk sample from the starter pit area with a head grade of 0.117% DTR nickel, as compared to the resource average of 0.129%.
ÂPrimary grind feed rates averaged 210 kg/h, with a total run time of over 80 hours.  In contrast, the Phase 1 pilot plant processed 3.6 tonnes of feed material over 23 hours of run time.  As previously reported, the shorter duration of the Phase 1 pilot was insufficient to reach steady state milling conditions due to the high density of awaruite and its influence on the recirculating load, while the Phase 3 pilot reached steady state conditions after processing 11 tonnes of material over 54 hours.  When steady state was reached, multiple surveys were conducted at primary grind sizes ranging from 80% passing 150 to 280 microns, leading to a robust dataset which supports the conclusions inferred from the Phase 1 pilot testing.
 Phase 3a – Primary Magnetic Separation Â
ÂAs demonstrated in the Phase 1 piloting, awaruite's high density (~8.6 specific gravity (" SG ")) presents an opportunity for preferentially grinding awaruite, versus the much less dense background of serpentine gangue minerals (approximately 2.5-3.0 SG). As a hydrocyclone classifies minerals based both on particle size and particle density, preferential grinding of awaruite was both expected and observed.  The preferential grinding of dense awaruite means that Baptiste can utilize a relatively coarse primary grind (target of 80% passing 275 microns for the PFS, versus 300 microns in the 2020 PEA) while achieving the metallurgical performance of a much finer grind, thus reducing circuit sizing, power consumption, and operating consumables.
ÂIn addition to demonstrating the benefits of preferential grinding of awaruite, additional pilot plant runs and ancillary bench-scale programs were completed to determine the impact of magnetic field strength on recovery. Note that the testwork supporting the 2020 PEA utilized relatively low intensity magnetic separation and did not thoroughly explore the benefits of increased field strength.
ÂThe impact of preferential grinding and magnetic field strength are summarized in Figure 2. The results clearly indicate a 0.5-1.5% increase in DTR nickel recovery due to increasing magnetic field strength from 1,200 to 1,800 Gauss.  Note that 1,800 Gauss is still sufficiently low to be classified as "low intensity" magnetic separation and as such does not require a significant change or cost increase in the magnetic technology required for industrial equipment.
ÂAlso seen in Figure 2, the pilot plant results clearly indicate an additional 0.5-1.0% recovery benefit attributed to preferential grinding, versus results achieved in bench-scale testing.  In aggregate, preferential grinding and increased magnetic field strength leads to a recovery increase of 2-3% at the coarse primary grind size targeted for the PFS (80% passing 275 microns).  For comparison, Figure 2 also presents the 90.1% DTR nickel stage recovery assumed in the 2020 PEA.  Additionally, Figure 2 also presents Phase 1 piloting results (96.9% DTR nickel recovery) which was conducted on a representative life-of-mine composite, illustrating the potential for further recovery improvements. The in-progress variability testwork (Phase 3b ) should provide further insight into this potential recovery improvement.
ÂÂ
   Â
 Phase 3a – Regrind and Cleaner Magnetic Separation Â
ÂFollowing the primary circuit pilot test, the regrind circuit pilot plant test was conducted. The objective of the regrind circuit is to further liberate awaruite and subsequently clean the concentrate by magnetic separation in order to produce a higher-grade "magnetics-rich" concentrate which can then be further upgraded by conventional froth flotation.
ÂSimilar to the primary circuit, the regrind circuit was set-up with closed circuit grinding using a hydrocyclone classifier, once again to take advantage of awaruite's high density and the resultant preferential grinding potential. While the preferential grinding phenomenon was expected, it was much more pronounced than in the primary circuit. Despite a total run time of 46 hours and a total regrind feed of 1.8 tonnes, steady state conditions were not achieved. At the time of shutdown, it was estimated that the DTR nickel recirculating load was 5600% and only approximately 40% of DTR nickel was sufficiently fine enough to have reported to cyclone overflow for magnetic separation cleaning.
ÂFor the approximately 40% of DTR nickel which was sufficiently ground to report to hydrocyclone overflow, the DTR nickel recovery in cleaner magnetic separation exceeded 99%, in line with the 100% stage recovery assumption in the 2020 PEA. The remaining DTR nickel recovered in the regrind circuit clean-out was batch ground and then subjected to magnetic separation, where DTR nickel recovery also exceeded 99%.
 Phase 3a – Flotation Â
ÂHaving created a magnetics-rich product through two stages of grinding and magnetic separation, the objective of froth flotation is to separate awaruite from magnetite. The cleaner magnetic separation concentrate produced from the regrind mill clean-out material was subjected to bench- and pilot-scale batch flotation as this material contained the majority of DTR nickel (60% of the regrind circuit feed). This material performed exceptionally well in flotation, with a 94% recovery to a final concentrate grading more than 65% nickel. This is inline with previous bench-scale flotation testwork results and the PEA's assumption of 94% flotation stage recovery to a 63% nickel concentrate.
ÂFlotation concentrate from the Corem work is now the feedstock for the current hydrometallurgical testing program, the results of which will be released in the second quarter of 2023.
ÂÂ Update on Phase 2 Flotation Testwork Â
 As indicated in the Company's July 27, 2022 news release, key flotation testwork results achieved during Phase 2 included confirmation of the ability to consistently produce very high-grade flotation concentrates and the potential for an alternative (lower-acid) flotation regime which could achieve similar metallurgical performance while reducing flotation operating costs and complexity. The Phase 2 news release indicated flotation testwork remained in progress, and an update on the results is presented herein.
ÂFurther optimization of the baseline flotation conditions resulted in a slight improvement in locked cycle testing, with flotation stage nickel recovery increasing from 87% to 88%. As indicated in the Company's July 27, 2022 news release, while recovery values are less than the PEA flotation stage recovery criteria of 94%, the current flotation results were impacted by the lower feed grade owing to the hold-up of nickel in the pilot plant grinding circuit. As comparable flotation tailings grades were observed across the current and historic flotation programs, and testwork continues to indicate that coarse, liberated awaruite is readily recoverable in flotation, the Company continues to anticipate recovery estimates would increase if the flotation feed material was more representative.
ÂAdditionally, locked cycle testwork on the alternative, lower-acid flotation regime achieved similar results to the Company's historical flotation conditions. This lower-acid regime has the potential to reduce acid consumption by approximately 25%. Fundamentally, testwork has now clearly identified two viable flotation regimes which can achieve similar and excellent metallurgical performance, thereby validating conventional froth flotation as a tool to produce very high-grade awaruite concentrates.
ÂÂ New Processing Option to Increase Nickel Recovery Â
 In addition to the ongoing flotation testwork, the Company is conducting a test program to demonstrate the potential to further improve nickel recovery through treating flotation tailings via leaching. The objective of this processing concept is to access any nickel contained in low-grade awaruite containing particles that would dilute the final concentrate grade or ultra-fine awaruite particles that may not respond as effectively to conventional froth flotation.
ÂTestwork to-date demonstrates that 65% of the nickel contained in flotation tailings can be readily leached using dilute sulphuric acid under ambient temperature and pressure conditions. The balance of unrecovered nickel (35%) is almost entirely composed of nickel contained within magnetite, either as locked particles or in solid solution. This indicates that the leaching process is extremely efficient for liberated or exposed awaruite particles. Nickel was selectively leached away from magnetite with minimal co-leaching of iron (around 2-3%) and very low free acidities in the leach liquor, which indicates the potential for low reagent consumptions. The majority of nickel in such a leach solution could readily be recovered as a mixed hydroxide precipitate (" MHP ") using simple and conventional unit operations. This would be a new product stream, in addition to the high-grade awaruite concentrate which would still constitute the vast majority (95% or greater) of nickel output.
ÂFlotation tailings nickel leaching represents a significant new opportunity to improve overall nickel recovery to match or exceed the 85% recovery assumed in the 2020 PEA. Based on results to date, it is estimated that DTR nickel recovery could be increased by 3-5% overall (from 82% to a minimum of 85%).
ÂÂ Qualified Person Â
 The metallurgical information in this news release has been prepared in accordance with Canadian regulatory requirements set out in National Instrument 43-101 Standards of Disclosures for Minerals Projects of the Canadian Securities Administrators ("NI 43-101") and supervised, reviewed, and verified by Jeffrey B. Austin, P.Eng., President of International Metallurgical and Environmental Inc., a "Qualified Person" as defined by NI 43-101 and the person who oversees metallurgical developments for FPX Nickel.
ÂÂ About the Decar Nickel District Â
 The Company's Decar Nickel District claims cover 245 km 2 of the Mount Sidney Williams ultramafic/ophiolite complex, 90 km northwest of Fort St. James in central British Columbia. The District is a two-hour drive from Fort St. James on a high-speed logging road.
ÂDecar hosts a greenfield discovery of nickel mineralization in the form of a naturally occurring nickel-iron alloy called awaruite (Ni 3 Fe), which is amenable to bulk-tonnage, open-pit mining. Awaruite mineralization has been identified in four target areas within this ophiolite complex, being the Baptiste Deposit, and the B, Sid and Van targets, as confirmed by drilling, petrographic examination, electron probe analyses and outcrop sampling on all four targets. Since 2010, approximately US $28 million has been spent on the exploration and development of Decar.
ÂOf the four targets in the Decar Nickel District, the Baptiste Deposit, which was initially the most accessible and had the biggest known surface footprint, has been the focus of diamond drilling since 2010, with a total of 99 holes and 33,700 m of drilling completed. The Sid target was tested with two holes in 2010 and the B target had a single hole drilled in 2011; all three holes intersected nickel-iron alloy mineralization over wide intervals with DTR nickel grades comparable to the Baptiste Deposit. In 2021, the Company executed a maiden drilling program at Van, which has returned promising results comparable with the strongest results at Baptiste. In 2022, the Company executed a step-out drilling program at Van which demonstrated a significant expansion of the 2021-identified mineralized zone.
ÂÂ About FPX Nickel Corp. Â
  FPX Nickel Corp. is focused on the exploration and development of the Decar Nickel District, located in central British Columbia , and other occurrences of the same unique style of naturally occurring nickel-iron alloy mineralization known as awaruite.
ÂOn behalf of FPX Nickel Corp.
 "Martin Turenne"
Martin Turenne , President, CEO and Director
  Forward-Looking Statements  Â
  Certain of the statements made and information contained herein is considered "forward-looking information" within the meaning of applicable Canadian securities laws. These statements address future events and conditions and so involve inherent risks and uncertainties, as disclosed in the Company's periodic filings with Canadian securities regulators. Actual results could differ from those currently projected. The Company does not assume the obligation to update any forward-looking statement. Â
ÂÂ Neither the TSX Venture Exchange nor its Regulation Services Provider accepts responsibility for the adequacy or accuracy of this release. Â
ÂÂ
 SOURCE FPX Nickel Corp.
Â
Â
ÂÂ View original content to download multimedia: https://www.newswire.ca/en/releases/archive/January2023/24/c7648.html Â