In their ISO-approved facilities, GMG's testing partner Supercool Asia Pacific Pty Ltd undertook two comparison tests to assess the impact of TXR in enhancing the operating efficiency of a cooling system. The equipment used in the tests was a new customised 4.3kW Refrigeration Unit with an electronic expansion valve with variability disabled (Figure 1 outlines the test room layout). The pre-TXR-treated condenser coil had an existing industry standard coating (as seen in Figure 2), on which tests were run. This condenser coil was then coated with TXR (as seen in Figure 2) and the same tests were run again.
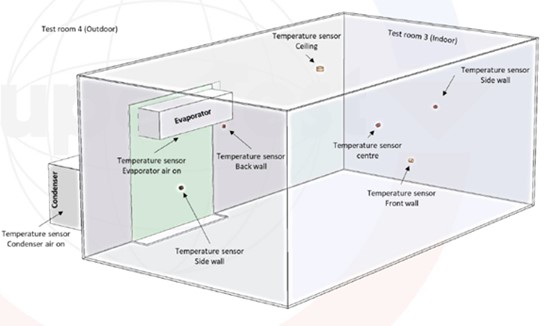
Figure 1: Test room for both comparison tests
To view an enhanced version of this graphic, please visit:
https://images.newsfilecorp.com/files/8082/168332_gmg_fig1_550.jpg
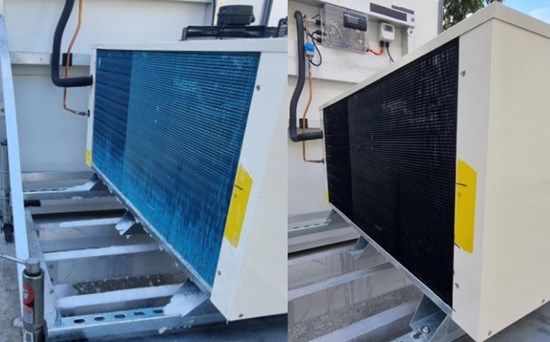
Figure 2: Condenser Coil Prior to THERMAL-XR® Coating (left) and
Condenser Coil Post THERMAL-XR® Coating (right)
To view an enhanced version of this graphic, please visit:
https://images.newsfilecorp.com/files/8082/168332_4404ddecd4a3fa18_002full.jpg
The first comparison test conducted was a Pull Down Test which assessed the time and energy required to reach a set temperature of 20C in the heat controlled room with an initial set temperature of 300C, controlled constant humidity level, and an outdoor temperature of 350C. This simulates a typical cold storage room with traffic subject to heat losses and required to cool down on multiple occasions to the set temperature. The quicker time to reach the set point cooling temperature, under the same conditions, highlights a reduction in energy consumption for the THERMAL-XR® coated condenser coil.
As seen in Table 1 the THERMAL-XR® coated coil resulted in 15.7% Energy Savings and a 16.1% time savings for the Pull Down test.
Test | Average Duration | Time Reduction | Average Power (kW) | Energy (kWh) | Energy Reduction |
Prior to THERMAL-XR® Coating | 1:10:41 | 16.1%▼ | 2.43 | 2.86 | 15.9%▼ |
Post THERMAL-XR® Coated | 0:59:17 | 2.44 | 2.41 |
Table 1: Pull Downtime and energy consumed prior to and post TXR coating.
The second comparison test was an uninterrupted 48-hour Temperature Cycle test. This tests the impact of TXR on maintaining a constant set point temperature (for example where there is no periodic access to a cool room). The test measured the energy required over a 48-hour period to keep a cooling set temperature of 20C in a heat-controlled room with an outside temperature of 350C and controlled constant humidity level. The lower amount of energy required by the THERMAL-XR® coated unit, under the same conditions, highlights the energy savings.
Table 2 shows the THERMAL-XR® coated coil delivered 4.69% Energy Savings for the 48-hour Temperature Cycle test.
48 hour Cycle Test - Power Consumption |
Between 0-48 hours | Average power (kW) | Energy (kWh) per 24 hours | Energy Reduction |
Prior to TXR coating | 1.77 | 85.10 | 3.71%▼ |
Post TXR coating | 1.71 | 81.95 |
|
Between 24- 48 hours | |
Prior to TXR coating | 1.76 | 42.14 | 4.13%▼ |
Post TXR coating | 1.68 | 40.39 |
|
Between 36- 48 hours | |
Prior to TXR coating | 1.76 | 21.09 | 4.69%▼ |
Post TXR coating | 1.68 | 20.10 |
Table 2: 48 Hour Cycle Energy Test Prior to vs Post TXR Coating
Full test results will be available on GMG's website.
Craig Nicol, GMG's CEO summarised as follows "The Energy Savings results of THERMAL-XR® in an independent, third party, ISO-accredited testing laboratory with two testing methodologies is very exciting. The graphene-enhanced heat transfer properties of THERMAL-XR® have demonstrated that the performance of a new coil can be enhanced. This has significant potential for our targeted market of new air conditioners or Original Equipment Manufacturers (OEMs), as well as our existing target market of installed air conditioners. It also helps put into context those GMG projects where results on old equipment have achieved even higher energy savings."
HEAT TRANSFER VERIFICATION
GMG has also been working with potential industrial customers to demonstrate the potential for improved heat management through the application of TXR. As part of this demonstration programme, GMG has commissioned the University of Queensland Materials Performance Consultancy to verify a number of heat transfer demonstrations.
GMG is pleased to report that the University of Queensland Materials Performance Consultancy ("UQMP") verified that GMG's THERMAL-XR®, demonstrations and results, when applied to Copper and Aluminium, changed the surface temperature when operating between 700C and 900C.
Copper Top Side Coating: Surface Temperature Reduction ~16%
As seen in Figure 3 GMG's THERMAL-XR®, when applied to a Copper plate, reduces the surface temperature by ~16% when operating between 700C and 900C compared with an uncoated plate. The chart below shows the temperature differences due to GMG's THERMAL-XR® when applied on a Copper plate with the same heat load.
As seen in Figure 4, when the THERMAL-XR® coating was applied to the top side copper plate, greater heat transfer was observed away from the common heat source (compared to the panel with no coating). Furthermore, the non-coated underside of the coated panel - being the side directly exposed to the heat source - remained approximately 16% cooler than the heat-exposed side of the uncoated panel, within the temperature range of 70°C to 90°C.
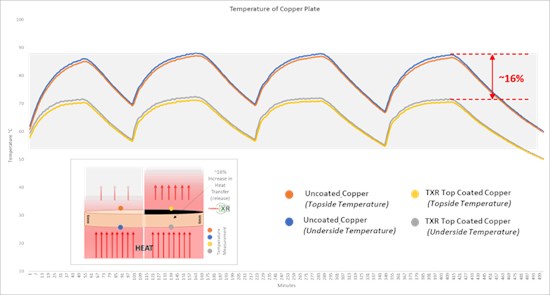
Figure 3: Temperature Reduction of TXR coating vs Uncoated
To view an enhanced version of this graphic, please visit:
https://images.newsfilecorp.com/files/8082/168332_4404ddecd4a3fa18_003full.jpg
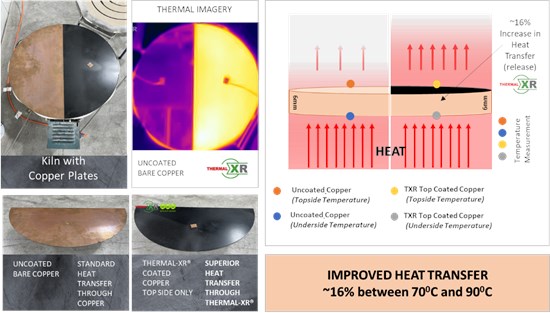
Figure 4: GMG's demonstration of THERMAL-XR® coating increases heat transfer when applied to Copper.
To view an enhanced version of this graphic, please visit:
https://images.newsfilecorp.com/files/8082/168332_4404ddecd4a3fa18_004full.jpg
Aluminium top side Coating: Surface Temperature Reduction ~15%
GMG previously reported the UQ had verified a ~ 15% reduction when TXR was applied to the top side of aluminium, compared to un-TXR coated material (please refer to press release of 20th December 2022).
Underside Coating | Aluminium and Copper: Surface Temperature Increase
In addition to these two 'top side' coating tests, GMG is also pleased to release the results of testing of GMG's THERMAL-XR® applied on the underside of both Aluminium and Copper (see Table 4), where the result was to see the underside of the plates increase in temperature, again following the same testing methodology.
Underside THERMAL-XR® Coating | Aluminium | Copper |
+15% | +29% |
Table 3: Temperature Increase from TXR Coating Underside.
Summary of All Results to Date for TXR coating of Aluminium and Copper, either top side or underside
These results, shown in Figure 5, are very encouraging in outlining the application of TXR for various heat management applications creating the potential for operating efficiency and / or energy savings.
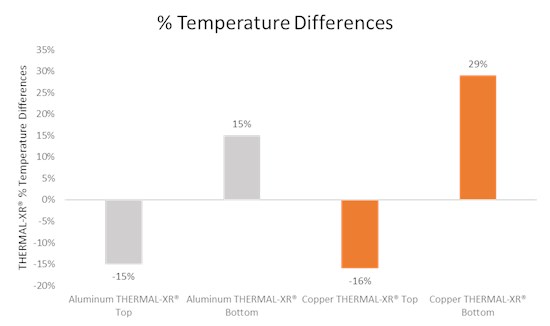
Figure 5: Temperature Increases and Decreases with TXR on Copper and Aluminium
To view an enhanced version of this graphic, please visit:
https://images.newsfilecorp.com/files/8082/168332_4404ddecd4a3fa18_005full.jpg
Relevance to Heat Exchangers in Air Conditioners and Industrial Applications
Copper and Aluminium are key metals used in HVAC-R equipment. This demonstration highlights that the external (top side) coating of the metal with THERMAL-XR® can improve heat transfer, potentially leading to Energy Savings because of reduced compressor and fan utilisation.
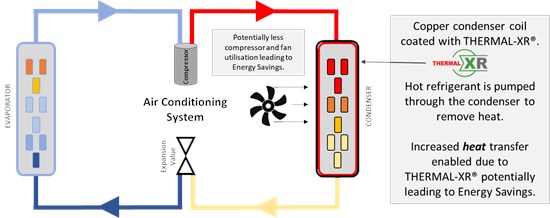
Figure 6
To view an enhanced version of this graphic, please visit:
https://images.newsfilecorp.com/files/8082/168332_4404ddecd4a3fa18_006full.jpg
Relevance to Other Potential Applications
The coating of metal with THERMAL-XR® exposed to a heat source (Under side coating) can potentially act as a heat sink to keep heat within a requirement.
"GMG's THERMAL-XR®'s ability to increase and reduce heat transfer is clear in this simple demonstration with operating temperatures between 70°C to 90°C. The graphene-enhanced heat transfer properties of THERMAL-XR® seemingly outweigh the traditional insulating effect of coatings when cooling. GMG believes the ability to increase or reduce temperature with a simple application of the technically advanced THERMAL-XR® can significantly contribute to improved performance and efficiency while reducing energy demand in a wide range of applications," stated by Managing Director and CEO, Craig Nicol.
THERMAL-XR® powered by the GMG Graphene coating system is a unique method of improving the conductivity of heat exchange surfaces, resulting in an efficiency improvement and a potential power reduction when applied to air conditioning condenser coils or other industrial processes needing heat transfer.
The performance of existing air conditioners can also be increased with THERMAL-XR® process fluids (PREP and ACTIVATE) which clean and remove corrosion on the coil before applying the THERMAL-XR® RESTORE.
GMG is undertaking further assessments on other metals used in heat transfer applications and at various temperature settings and will publish market updates from time to time on these.
GMG is working with a number of companies globally including four recently signed distributors in Asia (announced 24th May 2023) and direct sales for the HVAC-R maintenance market. Furthermore, GMG is engaging with various companies for direct selling of THERMAL-XR® for industrial applications with high energy requirements, and high emissions - including oil and gas production, power generation, liquified natural gas production, mining, and mineral processing.
In addition, a number of customers are interested in the protective features of TXR graphene-enhanced coating, especially in harsh environmental conditions.
GMG's 4 critical business objectives are:
- Produce Graphene and improve/scale the production process
- Build Revenue from Energy Savings Products
- Develop Next-Generation Battery
- Develop Supply Chain, Partners & Project Execution Capability
About The University of Queensland Materials Performance (UQMP)
UQ Materials Performance was founded in 1998 and has since grown to become one of Australia's leading materials engineering consultancies. Our mission statement:
UQ Materials Performance serves the needs of society by applying research methodologies to answer technical questions. UQMP strengthens UQ research by building relationships of trust with industry partners, systematising knowledge gained in short‐term projects, generating seed funding, and by direct involvement in structured research. UQMP inspires student learning by generating professional case studies which show their discipline in action.
UQMP has a dedicated team of engineers and industrial chemists with a wide range of experience and specialty skills. Our diverse and cross-disciplinary problem-solving approach also brings fresh perspectives to projects. Our team works closely together with our clients to clearly understand, define and tackle problems in a systematic yet direct manner. Our access to the world-class facilities of The University of Queensland puts us at the forefront of analytical science and engineering.
UQ Materials Performance operates out of The University of Queensland Advanced Engineering Building. We share the building with the Centre for Advanced Materials Processing and Manufacturing (AMPAM) and the School of Civil Engineering, allowing close collaboration on consulting and research projects.
About GMG
GMG is a disruptive Australian-based clean-tech company listed on the TSXV (TSXV: GMG) that produces graphene and hydrogen by cracking methane (natural gas) instead of mining graphite. By using the company's proprietary process, GMG can produce high quality, low cost, scalable, 'tuneable' and no/low contaminant graphene - enabling demonstrated cost and environmental improvements in a number of world-scale planet-friendly/clean-tech applications. Using this low input cost source of graphene, the Company is developing value-added products that target the massive energy efficiency and energy storage markets. The Company is pursuing additional opportunities for GMG Graphene, including developing next-generation batteries, collaborating with world-leading universities in Australia, and investigating the opportunity to enhance the performance of lubricant oil and performance-enhanced HVAC-R coating system.
For further information please contact:
- Craig Nicol, Chief Executive Officer and Managing Director of the Company at craig.nicol@graphenemg.com, +61 415 445 223
- Leo Karabelas at Focus Communications Investor Relations, leo@fcir.ca, +1 647 689 6041
www.graphenemg.com
Neither the TSX Venture Exchange nor its Regulation Services Provider (as that term is defined in the policies of the TSX Venture Exchange) accept responsibility for the adequacy or accuracy of this news release.
Cautionary Note Regarding Forward-Looking Statements
This news release includes certain statements and information that may constitute forward-looking information within the meaning of applicable Canadian securities laws. Forward-looking statements relate to future events or future performance and reflect the expectations or beliefs of management of the Company regarding future events. Generally, forward-looking statements and information can be identified by the use of forward-looking terminology such as "intends", "expects" or "anticipates", or variations of such words and phrases or statements that certain actions, events or results "may", "could", "should", "would" or will "potentially" or "likely" occur. This information and these statements, referred to herein as "forward‐looking statements", are not historical facts, are made as of the date of this news release and include without limitation, the impact of THERMAL-XR® on heat transfer and its potential applications and expected performance, management's expectations of the effects of Thermal-XR®, the intention of the Company to research, develop and produce certain products, and the Company's intention to engage third parties to assist in the distribution and sale of its products and statements.
Such forward-looking statements are based on a number of assumptions of management, including, without limitation, assumptions regarding the ability of the Company to achieve the expected results of its THERMAL-XR®, that the Company will be able to research, develop and produce certain products as anticipated, and that the Company will be able to engage third parties and develop relationships to assist in the development, distribution and sale of its products. Additionally, forward-looking information involve a variety of known and unknown risks, uncertainties and other factors which may cause the actual plans, intentions, activities, results, performance or achievements of GMG to be materially different from any future plans, intentions, activities, results, performance or achievements expressed or implied by such forward-looking statements. Such risks include, without limitation: the Company will not be able to use THERMAL-XR® as expected or the performance, safety profile and production and maintenance requirements of the THERMAL-XR® coating system will not be consistent with management's expectations, the impact of Thermal-XR® will not be consistent with management's expectations, the Company will not be able to research, develop and produce certain products, the Company will not be successful in engaging third parties and developing relationships to assist in the development, distribution and sale its products, public health crises such as the COVID-19 pandemic may adversely impact the Company's business and the ability of the Company to develop its products, risks relating to the extent and duration of the conflict in Eastern Europe and its impact on global markets, the volatility of global capital markets, political instability, the failure of the Company to attract and retain skilled personnel, unexpected development and production challenges, unanticipated costs and the risk factors set out under the heading "Risk Factors" in the Company's annual information form dated October 18, 2022 available for review on the Company's profile at www.sedar.com.
Although management of the Company has attempted to identify important factors that could cause actual results to differ materially from those contained in forward-looking statements or forward-looking information, there may be other factors that cause results not to be as anticipated, estimated or intended. There can be no assurance that such statements will prove to be accurate, as actual results and future events could differ materially from those anticipated in such statements. Accordingly, readers should not place undue reliance on forward-looking statements and forward-looking information. Readers are cautioned that reliance on such information may not be appropriate for other purposes. The Company does not undertake to update any forward-looking statement, forward-looking information or financial out-look that are incorporated by reference herein, except in accordance with applicable securities laws. We seek safe harbor.
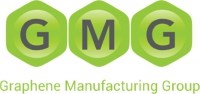
To view the source version of this press release, please visit https://www.newsfilecorp.com/release/168332
